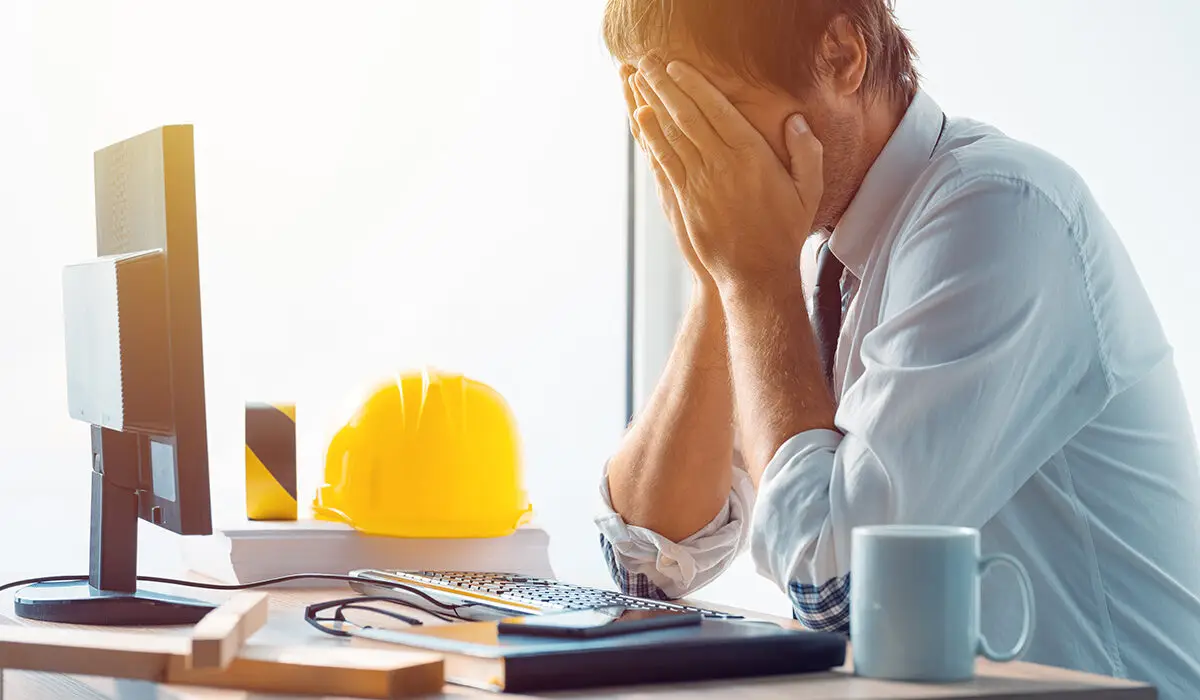
Construction is one of the most robust and resilient industries in the world, with an approximate value of $1.98 trillion in the United States alone in 2023, according to Statista. This critical sector provides economic growth and supports businesses, communities, and individuals across the globe. Yet this vital contributor to the economy is not without its risks and challenges.
According to an Arcadis 2022 Global Construction Disputes report, in 2021 the global average value of a dispute was $52.6 million. In North America, the average dispute value was $30.1 million with an average dispute length of 16.7 months. The highest value dispute reported by respondents was US$2 billion. Globally, sums in dispute tended toward a third of project CAPEX (32.3%), while contractors sought to extend schedules by more than half (58.8%) according to a 2023 HKA CRUX Insight report.
While not all contractors will experience disputes that large, any dispute can be incredibly costly. In fact, many disputes will come in under $1 million which will still be huge for the average contractor. For example, on a $20 million project, if it has 4% profit built-in ($800K) and you lose a $1 million dispute; you’re in the red $200K!
Disputes are caused by numerous reasons however, the top causes of project distress in the CRUX Insight report and others, had their roots in changes in scope and incomplete designs. Scope change was the top cause of claims and disputes on 38.8% of projects, while design errors – closely entwined with changing scope – impacted a fifth of projects. Three design-centric factors – incorrect, late or incomplete design information – are clustered within the global ranking’s top five causes. Further analysis revealed that this design triple whammy afflicted a greater proportion of projects overall (44.8%) than scope change alone (38.8%).
The “design triple whammy” is having a prodigious global impact on the industry. The good news is that advancements in technology, specifically in AI, are having an equally remarkable impact on mitigating this dilemma and others.
The one thing that all analysts can agree on is that more time invested up-front in planning, design, and coordination will result in achieving more successful outcomes. Unfortunately, today’s fast-track construction culture makes the prospect of slowing down unfathomable. As owners push to hit the ground running, the design phase is squeezed, leading to immature designs, inaccurate procurement, design conflicts, and scope gaps.
We all recognize that project teams may have to accept unfinished designs deemed “adequate to build” solely so construction can start on time with the idea that they’ll attempt to back-manage the accepted risk when the design continues to develop during construction. It’s in precisely this scenario, that AI is proving to be the early risk-mitigation tool needed to achieve more successful outcomes.
Leveraging AI technology such as Firmus automated design analysis software during the preconstruction phase can significantly reduce the design-induced risks, errors, and disputes associated with early design sets. Let’s look at 3 ways AI enables owners, builders, and design teams to mitigate the top risks early.
Identifying Design Issues
Today’s complex projects like hospitals and high-rise residential contracts include multiple trades and design disciplines across the buildings and systems. These projects require hundreds, if not thousands, ofdocuments, which can be a real challenge for those tasked with design coordination and manual design review processes.
Even the most proactive preconstruction teams can get stymied by the sheer volume of multi-discipline documentation requiring review at evermore truncated timelines. Utilizing AI to support and supplement these teams is a no-brainer. For example, AI-REVIEW’s automated construction document analysis can be completed in as little as 48 hours. The AI scans and detects issues in construction documents, such as incomplete design, scope gaps, and discrepancies. The resulting reporting provides precise and comprehensive issue identification and markups, optimizing workforce efficiency and ensuring nothing falls through the cracks.
Analyses include architectural, MEP, and overall document health checks, allowing project teams to quickly assess and respond to design risks before they impact your project budget, quality, or schedule.
Assessing the Impact of Identified Issues
Risk management practices, such as risk assessments, contingency planning, and effective project oversight, can help mitigate the impact of construction risks. Utilizing AI technology that can both identify design-related issues and assess their risk impact level[1] can be a big help. Project teams can quickly and easily review the identified issues and markups based on critical, medium, and low-priority categories to assess which risks are acceptable and which require immediate resolution.
3 surprisingly common design discrepancy examples that can cause big problems if not mitigated early:
- Incomplete or immature design
In a recent case study with Flintco, Michael Thole, Director of Corporate Quality discusses how “Flintco used Firmus in advance of putting a large glazing and curtain wall bid package on the street. The glazing schedule showed various curtain wall, storefront, and spandrel glass systems by color code to help identify placement. Firmus flagged multiple inconsistencies in the drawing set where curtainwall systems were incorrectly tagged as spandrel glass. Flintco’s preconstruction team was able to quickly review the design documents and verify the unique quantities necessary before purchasing.”
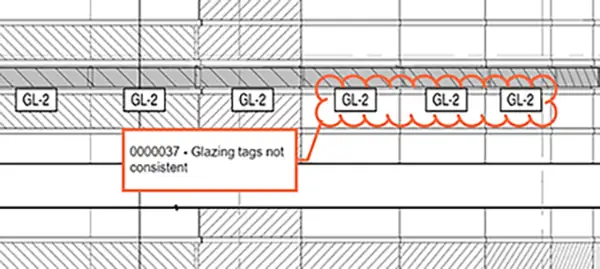
“The result improves “first-time quality” in the field,” said Thole. “Nobody wants to see a piece of plywood plugging a hole on a building façade because the glass order was inaccurate. The same scenario applies to doors and hardware schedules which are always a long lead item…”
- Cross-discipline design discrepancies
Take, for example, a student housing project with 425 student units, a GMP established on 50% CD documents, and a 3% contingency, with a total project value of $100,000,000. The architectural drawings contain a full finish schedule and elevations of all areas. The interior design drawings contain material call-outs and identification, and elevations of rooms with finishes.
In the construction phase, a discrepancy in the drawings is identified after the layout of rooms and walls is underway. All sleeves are completed, and plumbing and MEP systems are roughed in. The Architectural drawings call out paint but the Interior Design drawings call out tile in all 425 bathrooms. The tile walls are required to be set mortar. Depending on the stage of construction, the following rework costs would apply:
Cost of 425 Bathrooms: The price of the tile work in an after-contract estimate, is $700,000. ($1647/bathroom). There is also a rework requirement at each location:
- Cost to core any plumbing location-$250
- Cost to remove piping and relocate-$750
- Cost to replace drywall and or framing due to insufficient clearances-$2,300
Sub Total Cost per room $3,300
The total cost of the rework for the project: over $1,400,000
An AI analysis of thestudent housing project would have identified the discrepancies between the architectural and interior design plans. This would have allowed the project team to verify and confirm the correct call-outs and resolve the issue before procurement and construction.
- Incorrect design or missing information
Let’s take, for example, the coordination between connecting disciplines such as Civil to Plumbing and Electrical. In many cases, the interior design of plumbing systems is developed independent of the known site conditions. Late or uncoordinated connection to site utilities can result in major coordination and rework of systems in the building.
AI design review software can flag these types of design issues and POC for plumbing and electrical systems can be checked before ground break to verify locations, sizes, and elevations to ensure all systems are compatible.
_______________
[1] Impact levels are based on estimated cost, issue severity, frequency of occurrence, etc.
Collaboration
If a typical project has between 15 to 20 RFI’s per $1M in project value, and a single RFI takes an average of 9.7 days to receive a response, the loss of time and resulting delays and rework can be staggering. In fact, according to Navigant Construction Forum, 30% of the work performed by construction companies is rework.
Leveraging AI tools during the design and preconstruction stages can mitigate delays and greatly reduce the rework epidemic, especially those that allow for cooperative collaboration. After all, collaboration equals faster response times.
Nibbi Brothers General Contractors shared in a recent case study it has learned from decades of experience that the right approach is honest, collaborative, proactive, and supported by advanced technology. Nibbi knows that early team collaboration and proactive problem-solving can help maximize quality and avoid significant problems down the road.
“We recently had a project where the architect was impressed that we’re using an AI tool,” said Anita Hsieh, AIA QA Project Manager at Nibbi. “We started scanning drawings, maybe in the mid CDs, and overall, you can sense the level of drawing competency increases each time they submit. I think the architect appreciates having multiple tools at their disposal. It’s more like a team effort. It’s improved the way we interact with them over time. I also think they appreciate the thoroughness of the reviews we do and the time we’re putting into it. We’re all trying to get the set to be the best it can be.”
Cloud-based software like Firmus allows for unlimited users, allowing contractors and design firms to invite all relevant stakeholders to assigned projects for enhanced collaboration. Ensuring everyone has access to the same identified issues, document markups, and view comparisons enables a more cohesive approach, ultimately saving time and money.
Responding to Identified Issues
AI design review and risk analysis software create unexpected efficiencies, clarity, and faster response times for improved decision-making. Cloud-based software like Firmus includes unlimited users, allowing contractors to invite all relevant stakeholders to assigned projects for enhanced collaboration. Ensuring everyone has access to the same identified issues, document markups, and view comparisons enables a more cohesive approach, ultimately saving time and money.
In a recent article titled RFI’s Made Easier. For Everyone, utilizing AI design review software to identify, respond to, and expedite the response to identified issues is explored. What was found is that preconstruction and design teams can leverage AI to increase productivity and resource optimization while reducing their project and business risk. And when teams can focus on the strategic aspects of project design and constructability, employee satisfaction and retention increase.
AI tools can also help improve project clarity and decision-making. One of the basic tenets of the RFI process is to make clear requests. AI tools like Firmus, designed by construction industry experts in collaboration with architects can provide clear document markups with the supporting context needed to quickly and easily review the identified issue(s). These expert markups combined with drawing overlays where applicable, make the RFI review, response, and resolution easier for everyone involved. The natural result is higher project quality, cost-controlling, and clarity.
There is no question that design-related issues can have a major impact on preconstruction processes, bid and procurement accuracy, and the progress of a project, leading to errors, cost overruns, delays, and disputes. Analysts agree investing more resources earlier could preempt many of the most common disputes. The good news is that with advancements in construction technology, project teams can identify, assess, and manage project risks early and proactively. AI is bringing forth an era where risk is minimized, and trust is maximized.